Will Not Hold System Pressure Without Drive
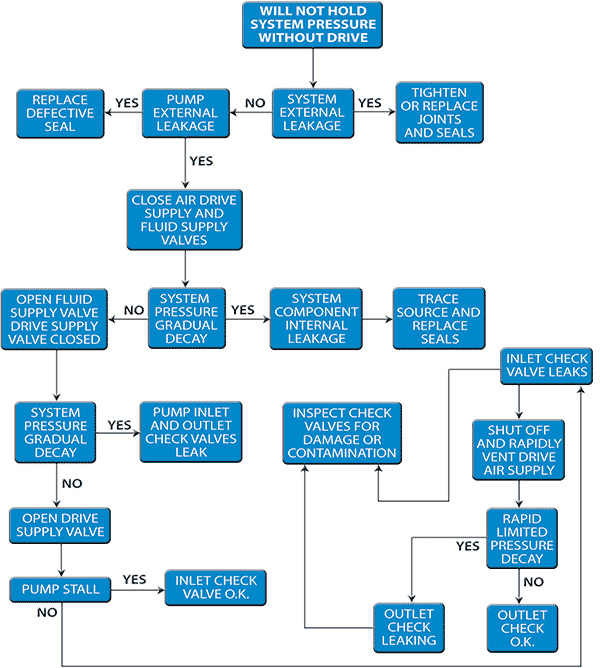
WILL NOT HOLD PRESSURE WITHOUT DRIVE AIR:
SYMPTOMS:
Venting drive pressure results in a momentary drop in system pressure, or a steady rapid decline in system pressure, with a small system volume). Larger system volumes will not be as noticeable, since a small gas leak will take a longer time to show the effect because of gas compressibility.
THEORY OF CAUSE:
In a "normal" situation with a "leak free" system and a "good" booster, the system pressure will have no significant decay when the booster is stopped and the air drive vented. (Note that the booster check valves are designed for operation of the booster.
Long duration sealing is NOT a requirement. Therefore, it should not be used for “long duration” maintenance of system pressure when the booster is not operational. If this is desired, an additional check valve or shutoff valve should be installed to isolate the booster when not in use). The outlet check valve will prevent return of transferred gas, and a “leak free” system will prevent pressure loss. Pressure will remain relatively constant, except for a slight decrease due to cooling. Since gas leakage in the system CAN occur, it is necessary to eliminate that possibility before looking for booster problems.
The following items can cause the condition:
a. System external leakage (loose or defective fittings)
b. System internal leakage (through valve seats, cylinder piston seals or relief valves)
c. Booster outlet check leakage (can cause momentary drop, but not continued rapid decline in pressure, for small system volumes, since only booster displacement and piston seal leakage is available as a leak path for the system gas).
d. Booster outlet AND inlet check valve leakage (will cause momentary drop and continued decline in pressure for small system volumes, as gas leaks through both check valves back to the gas supply line.
TROUBLE SHOOTING METHODS:
Adjust air drive pressure to the value which will just barely maintain system pressure (stall).
Verify no external leakage of gas at the booster and all system joints and components with the system maintained at operating pressure and the booster operational.
Shut off both the air drive pressure supply and gas supply valves. Uncouple the gas supply line at the booster inlet.
If the system pressure continues to decay without stopping, and there is no evidence of leakage at the booster inlet, gas barrel vent (piston seal Leakage), or rod seal leakage, then there is most likely an internal leakage in a system component.
If there is leakage at the gas inlet, then both inlet and outlet checks are leaking. If there is no leakage at the gas inlet, but the gas barrel vent shows leakage, then the outlet check and the piston seal are leaking. Verify that the leakages sufficient to warrant service to the booster. Some small leakage of any dynamic seal can be expected. If the downstream system volume is small, a leakage rate that is tolerable for most applications may result in a small decay rate, and may not warrant the cost of repairs until it increases to a level that affects ability to pressurize in a reasonable time, or the cost of the gas being pumped becomes a significant factor (i.e. – SF6 gas). Addition of a tight sealing check valve in series with the booster outlet check valve can also eliminate the effect of this leakage and permit a greater time between service periods.
If there is no internal or external leakage in the booster, then there is an internal component leakage in the downstream system.